"An old-time quilt maker used a needle as often, as easily, as casually as we use a telephone: it was her duty, her comfort, her companion, her mode of self-expression."
Today each quilter has her favorite brand and very good reasons to back up that assertion. She’ll try different ones and discuss what her mentor quilter uses, but when she makes her decision; she’s loyal to it, until someone can show her a better needle. Otherwise, she and her needle are a team. Airport personnel now see this needle as a weapon.
Who would have thought this vehicle of calm and warmth could also be a thing to fear? It started me thinking about how the precious needle is made
The first sewing needles were hand-made out of bone, over 17,000 years ago by western Europeans and central Asians. |
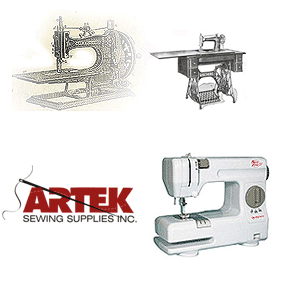
|
In the 20th century, more than 20 steps were taken to manufacture an enormous variety of sewing needle, for hands and machines. Sewing needles are made two at a time, from coils of steel wire. The wire is straightened and cut to the length of two. Through a grinding process, points are formed at both ends. Using a grindstone, the needle is turned repeatedly until the point is fine and even. This is one of the places on a needle where one might see a difference between a high vs. lower quality needle. If the point is not sharp or there is a burr, then your quilting will be more difficult to accomplish, if not impossible. The same would be true of the shaft.
Next, the eyes are stamped into the wire near the middle; two flat areas are stamped first, with the perfectly sized eyes punched through by another machine. Another piece of wire is drawn through the holes (like dental floss after a cleaning) so when the needle wire is cut apart, two needles remain, hanging from the wire. Their heads are smoothed and rounded. Their bodies are checked for straightness, tempered for toughness, and polished for smoothness. Quality control and a wide variety of packaging vehicles finish the process before they are shipped to their future owners. I wonder if needlemaking will change in the 21st century?
I did get an eyeless needle one time. No, it wasn’t a headless pin. It had an eye dent. Come to think of it, batting has body, thread has weight, fabric has a hand, dye bleeds, machines hum, and quilter’s have the smarts to make them all work together. Ok class, that’s the end of this anatomy artek.com
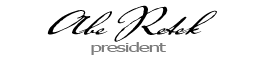
|